Features
This series uses a surface hardening method, which improves wear resistance by hardening the work surface while retaining softness within the work to allow energy loaded on the surface to be absorbed internally.
This method is used in carburizing and quenching, carbonitriding and gas soft nitriding.
SADSmall Gas Curburizing Furnace

High-performance gas carburizing furnace for wide variety, small-lot production
Applications | Quenching of oil-quenched steel, carburizing and quenching, carbonitriding and annealing |
---|---|
Features |
|
Temperature | 800 to 950℃ |
Treated weight | 60 to 100 kg/gross |
Atmosphere | N2+CH3OH+C3H8 |
ELPNPot Type Gas Nitriding Furnace
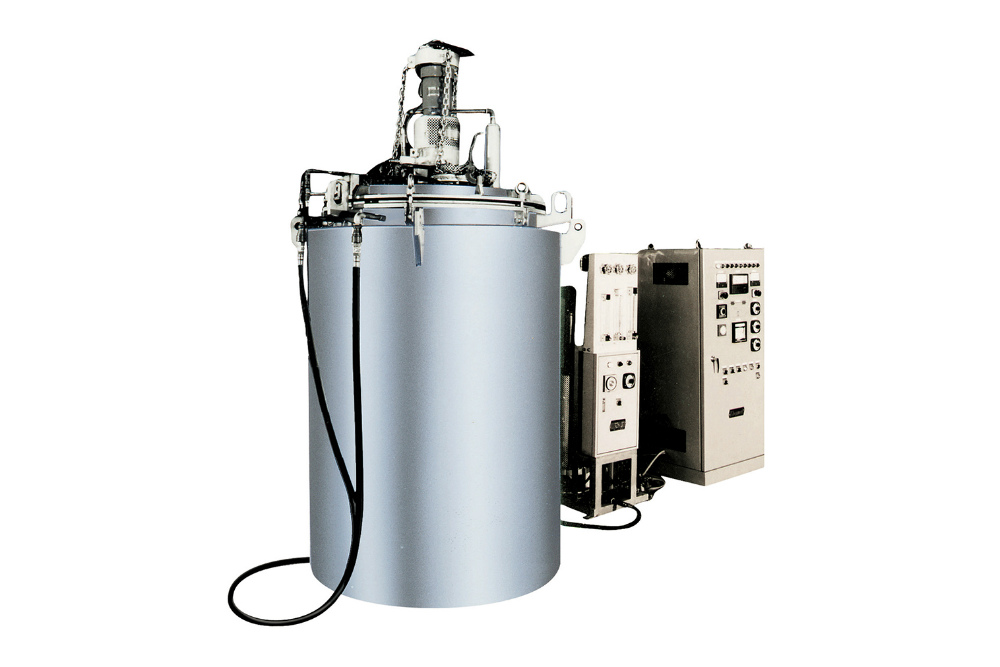
Surface hardening through nitriding for improved wear resistance of precision parts
Applications | Hard nitriding and soft nitriding of dies and die parts |
---|---|
Features |
|
Temperature | 400 to 600℃ |
Treated weight | 50 to 300 kg/gross |
Atmosphere | NH3+CO2 after N2 purge |
RAVNHorizontal Vacuum Nitriding Furnace
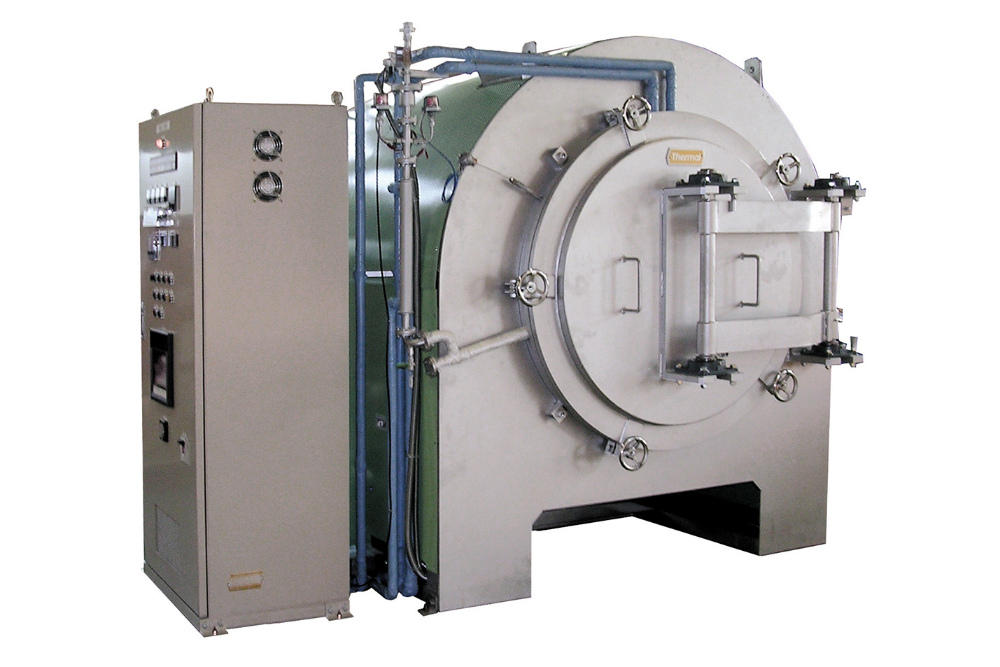
Surface hardening through nitriding for improved wear resistance of precision parts
Applications | Hard nitriding and soft nitriding of dies and die parts |
---|---|
Features |
|
Temperature | 400 to 600℃ |
Treated weight | 100 to 300 kg/gross |
Atmosphere | N2+CO2+NH3 after vacuum substitution |
Next-Generation Nitriding Potential Control System Equipped with NITRONAVI® RAV-N
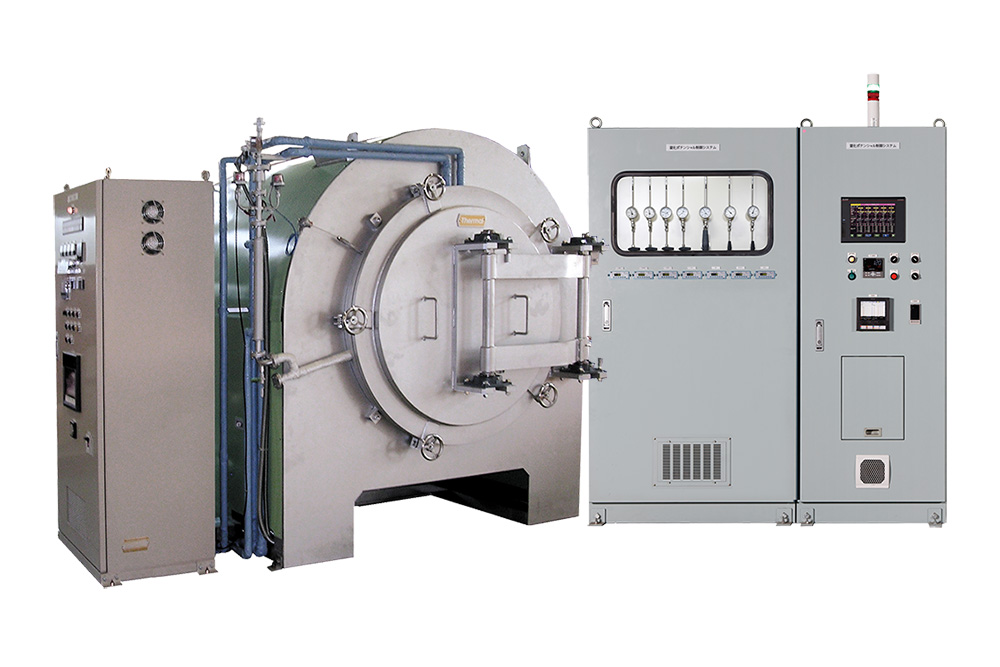
High-quality surface hardening for precision components through controlled nitriding processing
Applications | Controlled nitriding for various precision components, structural parts, molds, and mold parts |
---|---|
Features |
|
Temperature | 100 to 650℃ |
Treated weight | 50 to 1300 kg/gross |
Atmosphere | After vacuum purge Various gases |
More about Equipped with NITRONAVI® RAV-N
Details